应用案例
您当前的位置:产品应用
全自动内外螺丝加工机
全自动内外螺丝加工机
【申请公布号:CN107775118A;申请权利人:河北建支铸造集团有限公司;发明设计人: 任劲峰; 任福艳; 陈凤宇; 郝术洋; 陈秀军;】
摘要:
本发明公开了一种全自动内外螺丝加工机,由控制系统、加工系统、振动供料系统、振动运料系统、移料系统组成:加工系统包括内丝攻丝头、外丝攻丝头、固定卡具;振动供料系统包括供料振动源、振动供料盘,振动供料盘中设计有螺旋状走料路径;振动运料系统包括振动运料通道、运料振动源、挡件气缸、挡件闸板、检测开关;移料系统包括立架、伺服电机、横向滑轨,还包括由滑动架、同步带、升降气缸、旋转气缸座、旋转气缸、连接板、手指气缸构成的机械手,本发明从管件供料、运料直至装卡、内外螺丝加工全部实现了自动化操控,可大幅提高工作效率,节省生产成本,降低废品率,消除生产安全隐患。
主权项:
全自动内外螺丝加工机,由控制系统、加工系统、振动供料系统、振动运料系统、移料系统组成:控制系统采用PLC程序实现对相关部件工作状态的自动控制;加工系统设置在机台(5)上的加工位,包括内丝攻丝头(22)、外丝攻丝头(23)、固定卡具(24),内、外攻丝头相对设置在同一轴线上,内、外攻丝头之间设置有固定卡具(24);其特征是,振动供料系统位于整机一侧,包括供料振动源(1)、振动供料盘(2),振动供料盘(2)固定在供料振动源(1)之上,振动供料盘(2)中设计有螺旋状走料路径(3),振动供料盘(2)的走料路径终端与振动运料通道(6)的进料端相衔接,在走料路径(3)终端设计有选料段(4);振动运料系统设置在机台(5)上,包括振动运料通道(6)、运料振动源(7)、挡件气缸(8)、挡件闸板(9)、检测开关(10),振动运料通道(6)的进料端与振动供料盘(2)的走料路径终端相衔接,振动运料通道(6)的底部固定有运料振动源(7),挡件气缸(8)通过支板(11)设置在振动运料通道(6)出料端的上方,挡件气缸(8)连接有挡件闸板(9),检测开关(10)设置在振动运料通道(6)出料端的下面;移料系统设置在机台(5)上与振动运料系统左右相对,包括立架(12)、伺服电机(13)、横向滑轨(14),还包括由滑动架(15)、同步带(16)、升降气缸(17)、旋转气缸座(18)、旋转气缸(19)、连接板(20)、手指气缸(21)构成的机械手,立架(12)上固定有伺服电机(13)和横向滑轨(14),滑动架(15)滑动设置在横向滑轨(14)上并连接着伺服电机轮上的同步带(16),滑动架(15)的上方固定有升降气缸(17),旋转气缸座(18)的一侧滑动设置在滑动架(15)一侧的纵向滑轨上,旋转气缸座(18)的上面连接在升降气缸轴端,旋转气缸座(18)的对角位轴式连接着旋转气缸(19),旋转气缸(19)通过具有固定角度的连接板(20)连接着手指气缸(21)。
要求:
1.全自动内外螺丝加工机,由控制系统、加工系统、振动供料系统、振动运料系统、移料系统组成:
控制系统采用PLC程序实现对相关部件工作状态的自动控制;加工系统设置在机台(5)上的加工位,包括内丝攻丝头(22)、外丝攻丝头(23)、固定卡具(24),内、外攻丝头相对设置在同一轴线上,内、外攻丝头之间设置有固定卡具(24);其特征是,振动供料系统位于整机一侧,包括供料振动源(1)、振动供料盘(2),振动供料盘(2)固定在供料振动源(1)之上,振动供料盘(2)中设计有螺旋状走料路径(3),振动供料盘(2)的走料路径终端与振动运料通道(6)的进料端相衔接,在走料路径(3)终端设计有选料段(4);振动运料系统设置在机台(5)上,包括振动运料通道(6)、运料振动源(7)、挡件气缸(8)、挡件闸板(9)、检测开关(10),振动运料通道(6)的进料端与振动供料盘(2)的走料路径终端相衔接,振动运料通道(6)的底部固定有运料振动源(7),挡件气缸(8)通过支板(11)设置在振动运料通道(6)出料端的上方,挡件气缸(8)连接有挡件闸板(9),检测开关(10)设置在振动运料通道(6)出料端的下面;移料系统设置在机台(5)上与振动运料系统左右相对,包括立架(12)、伺服电机(13)、横向滑轨(14),还包括由滑动架(15)、同步带(16)、升降气缸(17)、旋转气缸座(18)、旋转气缸(19)、连接板(20)、手指气缸(21)构成的机械手,立架(12)上固定有伺服电机(13)和横向滑轨(14),滑动架(15)滑动设置在横向滑轨(14)上并连接着伺服电机轮上的同步带(16),滑动架(15)的上方固定有升降气缸(17),旋转气缸座(18)的一侧滑动设置在滑动架(15)一侧的纵向滑轨上,旋转气缸座(18)的上面连接在升降气缸轴端,旋转气缸座(18)的对角位轴式连接着旋转气缸(19),旋转气缸(19)通过具有固定角度的连接板(20)连接着手指气缸(21)。
全自动内外螺丝加工机
技术领域
本发明涉及一种管螺纹自动化加工设备,特别是一种全自动内外螺丝加工机。
背景技术
目前,加工可锻铸铁管件的内、外螺丝都是采用普通的双头攻丝机,这种攻丝机是在主机的中间部位装有卡具,卡具左右两边各有一个攻丝头,管件装卡到位后,左右攻丝头旋转进尺完成内、外螺纹加工,由于这种攻丝机是由工人在卡具和攻丝头不停地反复运动中手工完成管件的装卡,极易发生伤手事故,为避免伤手,操作者必须手持专用铁钳夹住管件进行装卡操作,即使如此,操作时稍有疏忽就有伤及操作者的危险,由此可见,现有的内外螺丝加工设备不仅工作效率低,劳动强度大,而且存在生产安全隐患。
发明内容
为克服传统式内外螺丝加工设备工作效率低,劳动强度大,易发生安全事故的缺陷,本发明提供一种全自动内外螺丝加工机。
本发明的技术方案是,全自动内外螺丝加工机由控制系统、加工系统、振动供料系统、振动运料系统、移料系统组成:
控制系统采用PLC程序实现对相关部件工作状态的自动控制;加工系统设置在机台上的加工位,包括内丝攻丝头、外丝攻丝头、固定卡具,内、外攻丝头相对设置在同一轴线上,内、外攻丝头之间设置有固定卡具;振动供料系统位于整机一侧,包括供料振动源、振动供料盘,振动供料盘固定在供料振动源之上,振动供料盘中设计有螺旋状走料路径,振动供料盘的走料路径终端与振动运料通道的进料端相衔接,在走料路径终端设计有选料段;振动运料系统设置在机台上,包括振动运料通道、运料振动源、挡件气缸、挡件闸板、检测开关,振动运料通道的进料端与振动供料盘的走料路径终端相衔接,振动运料通道的底部固定有运料振动源,挡件气缸通过支板设置在振动运料通道出料端的上方,挡件气缸连接有挡件闸板,检测开关设置在振动运料通道出料端的下面;移料系统设置在机台上与振动运料系统左右相对,包括立架、伺服电机、横向滑轨,还包括由滑动架、同步带、升降气缸、旋转气缸座、旋转气缸、连接板、手指气缸构成的机械手,立架上固定有伺服电机和横向滑轨,滑动架滑动设置在横向滑轨上并连接着伺服电机轮上的同步带,滑动架的上方固定有升降气缸,旋转气缸座的一侧滑动设置在滑动架一侧的纵向滑轨上,旋转气缸座的上面连接在升降气缸轴端,旋转气缸座的对角位轴式连接着旋转气缸,旋转气缸通过具有固定角度的连接板连接着手指气缸。
所述振动供料系统是通过供料振动源对振动供料盘的振动力,推动管件自动沿螺旋状走料路径进入振动运料通道;
所述选料段其特点是走料路径到此变成了侧向浅槽,当管件走到此段时可以实现自动选择料口方向,以保证进入振动运料通道的管件的料口方向一致,因管件的一端是待攻内丝的大外径料口,而另一端则是待攻外丝的小外径料口,当管件沿走料路径走到选料段时,小料口朝外的管件会被振动着顺利进入振动运料通道,而大料口朝外的管件会因为大料口一端失重而自动跌落到振动供料盘中继续待选;
所述振动运料系统,是把进入振动运料通道的管件,由运料振动源的振动力,推动管件沿振动运料通道继续前行,当第一个管件走到振动运料通道末端的机械手取件位置并被检测开关检测到时,挡件气缸使挡件闸板落下挡住后面继续前行的管件,以便机械手夹取检测到的管件;
所述移料系统是将管件移到加工位,当检测开关检测到有管件到达机械手取件位置时,挡件闸板下落,机械手下移将检测到的管件夹紧后提升到合适高度,在同步带的带动下平移到加工位上方,尔后旋转气缸带动手指气缸旋转90°后,机械手被升降气缸推动下移将管件送到固定卡具内后,返回取件位置的上方;
所述加工系统,是固定卡具卡紧加工管件后,由内丝攻丝头、外丝攻丝头从两头同时旋转进刀完成管件两头内、外螺丝的加工。
本发明实现了管件内外螺丝加工的全自动化,摒弃了频繁的手工装卡操作方式,与普通的双头攻丝机相比具有以下特点:
1、自动化程度高,可大幅提高加工效率,节省生产成本,一个操作工可同时操控4台机床,提高工作效率3-4倍,节省工资开支60%以上;
2、机器动作精准,可提高优质品率,减少废品损失3%以上;
3、可避免伤手事故,消除生产安全隐患。
附图说明
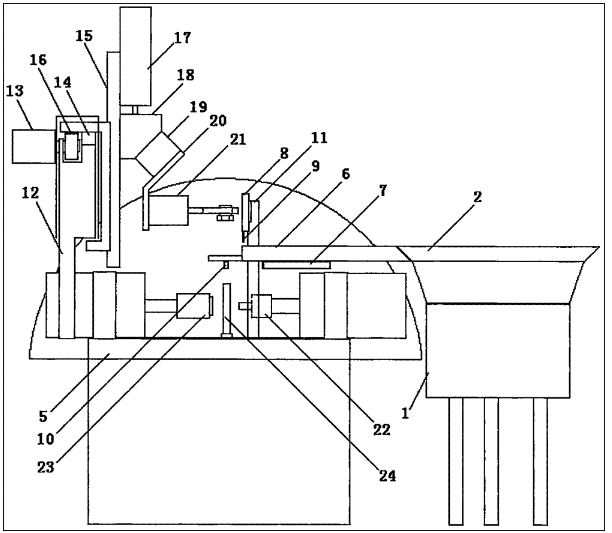
图1是本发明的正视图,图中机械手处于平行夹起管件上移的状态;
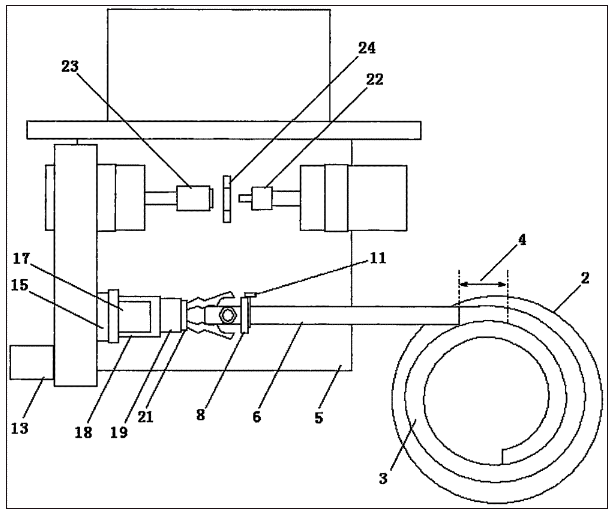
图2是本发明的俯视图,图中机械手已下移到振动运料通道末端的机械手取件位置欲夹取被检测到的管件。
图中:供料振动源1、振动供料盘2、走料路径3、选料段4、机台5、振动运料通道6、运料振动源7、挡件气缸8、挡件闸板9、检测开关10、支板11、立架12、伺服电机13、横向滑轨14、滑动架15、同步带16、升降气缸17、旋转气缸座18、旋转气缸19、连接板20、手指气缸21、内丝攻丝头22、外丝攻丝头23、固定卡具24
具体实施方式
下面对照附图通过实施例对本发明进行详细描述。
如图1、2所示,本发明全自动内外螺丝加工机由控制系统、加工系统、振动供料系统、振动运料系统、移料系统组成:
控制系统采用PLC程序实现对相关部件工作状态的自动控制;加工系统设置在机台5上的加工位,包括内丝攻丝头22、外丝攻丝头23、固定卡具24,内、外攻丝头相对设置在同一轴线上,内、外攻丝头之间设置有固定卡具24;振动供料系统位于整机一侧,包括供料振动源1、振动供料盘2,振动供料盘2固定在供料振动源1之上,振动供料盘2中设计有螺旋状走料路径3,振动供料盘2的走料路径终端与振动运料通道6的进料端相衔接,在走料路径3终端设计有选料段4;振动运料系统设置在机台5上,包括振动运料通道6、运料振动源7、挡件气缸8、挡件闸板9、检测开关10,振动运料通道6的进料端与振动供料盘2的走料路径终端相衔接,振动运料通道6的底部固定有运料振动源7,挡件气缸8通过支板11设置在振动运料通道6出料端的上方,挡件气缸8连接有挡件闸板9,检测开关10设置在振动运料通道6出料端的下面;移料系统设置在机台5上与振动运料系统左右相对,包括立架12、伺服电机13、横向滑轨14,还包括由滑动架15、同步带16、升降气缸17、旋转气缸座18、旋转气缸19、连接板20、手指气缸21构成的机械手,立架12上固定有伺服电机13和横向滑轨14,滑动架15滑动设置在横向滑轨14上并连接着伺服电机轮上的同步带16,滑动架15的上方固定有升降气缸17,旋转气缸座18的一侧滑动设置在滑动架15一侧的纵向滑轨上,旋转气缸座18的上面连接在升降气缸轴端,旋转气缸座18的对角位轴式连接着旋转气缸19,旋转气缸19通过具有固定角度的连接板20连接着手指气缸21。
实施例:
将管件装入振动供料盘2,开机,供料振动源1发出的振动力推动振动供料盘2内的管件沿走料路径3依次前行,当管件走到走料路径3终端的选料段4时,小料口朝外的管件被振动着进入振动运料通道6,而大料口朝外的管件会因为大料口一端失重而自动跌落到振动供料盘2中;当管件进入振动运料通道6时,振动运料通道6底部的运料振动源7产生的振动力推着管件前行,当第一个管件走到振动运料通道6末端的机械手取件位置并被检测开关10检测到时,挡件气缸8使挡件闸板9落下挡住后面继续前行的管件,以便机械手夹取检测到的管件;
挡件闸板9下落后,处于上方的机械手在升降气缸17的推动下下移,手指气缸21动作使其上的手指平行张开将管件夹紧,然后在升降气缸17的拉动下提升到合适高度,随之伺服电机13启动,通过同步带16的运转带动夹有管件的机械手平移到加工位上方,旋转气缸19带动手指气缸21旋转90°,使手指气缸21夹着管件的手指垂直朝下,管件与固定卡具24处于同轴状态,此时升降气缸17再次推动机械手下移,使管件进入固定卡具24内被卡紧,手指气缸21动作使其上的手指张开松开管件,随之在升降气缸17的拉动下机械手上移,旋转气缸19带动手指气缸21反向旋转90°,使手指气缸21的手指还原到水平状态,再由伺服电机13带动同步带16使机械手横移到取件位置的上方,被卡紧在固定卡具24内的管件由内丝攻丝头22、外丝攻丝头23从两头同时旋转进刀完成管件两头内、外螺丝的加工。
【申请公布号:CN107775118A;申请权利人:河北建支铸造集团有限公司;发明设计人: 任劲峰; 任福艳; 陈凤宇; 郝术洋; 陈秀军;】
摘要:
本发明公开了一种全自动内外螺丝加工机,由控制系统、加工系统、振动供料系统、振动运料系统、移料系统组成:加工系统包括内丝攻丝头、外丝攻丝头、固定卡具;振动供料系统包括供料振动源、振动供料盘,振动供料盘中设计有螺旋状走料路径;振动运料系统包括振动运料通道、运料振动源、挡件气缸、挡件闸板、检测开关;移料系统包括立架、伺服电机、横向滑轨,还包括由滑动架、同步带、升降气缸、旋转气缸座、旋转气缸、连接板、手指气缸构成的机械手,本发明从管件供料、运料直至装卡、内外螺丝加工全部实现了自动化操控,可大幅提高工作效率,节省生产成本,降低废品率,消除生产安全隐患。
主权项:
全自动内外螺丝加工机,由控制系统、加工系统、振动供料系统、振动运料系统、移料系统组成:控制系统采用PLC程序实现对相关部件工作状态的自动控制;加工系统设置在机台(5)上的加工位,包括内丝攻丝头(22)、外丝攻丝头(23)、固定卡具(24),内、外攻丝头相对设置在同一轴线上,内、外攻丝头之间设置有固定卡具(24);其特征是,振动供料系统位于整机一侧,包括供料振动源(1)、振动供料盘(2),振动供料盘(2)固定在供料振动源(1)之上,振动供料盘(2)中设计有螺旋状走料路径(3),振动供料盘(2)的走料路径终端与振动运料通道(6)的进料端相衔接,在走料路径(3)终端设计有选料段(4);振动运料系统设置在机台(5)上,包括振动运料通道(6)、运料振动源(7)、挡件气缸(8)、挡件闸板(9)、检测开关(10),振动运料通道(6)的进料端与振动供料盘(2)的走料路径终端相衔接,振动运料通道(6)的底部固定有运料振动源(7),挡件气缸(8)通过支板(11)设置在振动运料通道(6)出料端的上方,挡件气缸(8)连接有挡件闸板(9),检测开关(10)设置在振动运料通道(6)出料端的下面;移料系统设置在机台(5)上与振动运料系统左右相对,包括立架(12)、伺服电机(13)、横向滑轨(14),还包括由滑动架(15)、同步带(16)、升降气缸(17)、旋转气缸座(18)、旋转气缸(19)、连接板(20)、手指气缸(21)构成的机械手,立架(12)上固定有伺服电机(13)和横向滑轨(14),滑动架(15)滑动设置在横向滑轨(14)上并连接着伺服电机轮上的同步带(16),滑动架(15)的上方固定有升降气缸(17),旋转气缸座(18)的一侧滑动设置在滑动架(15)一侧的纵向滑轨上,旋转气缸座(18)的上面连接在升降气缸轴端,旋转气缸座(18)的对角位轴式连接着旋转气缸(19),旋转气缸(19)通过具有固定角度的连接板(20)连接着手指气缸(21)。
要求:
1.全自动内外螺丝加工机,由控制系统、加工系统、振动供料系统、振动运料系统、移料系统组成:
控制系统采用PLC程序实现对相关部件工作状态的自动控制;加工系统设置在机台(5)上的加工位,包括内丝攻丝头(22)、外丝攻丝头(23)、固定卡具(24),内、外攻丝头相对设置在同一轴线上,内、外攻丝头之间设置有固定卡具(24);其特征是,振动供料系统位于整机一侧,包括供料振动源(1)、振动供料盘(2),振动供料盘(2)固定在供料振动源(1)之上,振动供料盘(2)中设计有螺旋状走料路径(3),振动供料盘(2)的走料路径终端与振动运料通道(6)的进料端相衔接,在走料路径(3)终端设计有选料段(4);振动运料系统设置在机台(5)上,包括振动运料通道(6)、运料振动源(7)、挡件气缸(8)、挡件闸板(9)、检测开关(10),振动运料通道(6)的进料端与振动供料盘(2)的走料路径终端相衔接,振动运料通道(6)的底部固定有运料振动源(7),挡件气缸(8)通过支板(11)设置在振动运料通道(6)出料端的上方,挡件气缸(8)连接有挡件闸板(9),检测开关(10)设置在振动运料通道(6)出料端的下面;移料系统设置在机台(5)上与振动运料系统左右相对,包括立架(12)、伺服电机(13)、横向滑轨(14),还包括由滑动架(15)、同步带(16)、升降气缸(17)、旋转气缸座(18)、旋转气缸(19)、连接板(20)、手指气缸(21)构成的机械手,立架(12)上固定有伺服电机(13)和横向滑轨(14),滑动架(15)滑动设置在横向滑轨(14)上并连接着伺服电机轮上的同步带(16),滑动架(15)的上方固定有升降气缸(17),旋转气缸座(18)的一侧滑动设置在滑动架(15)一侧的纵向滑轨上,旋转气缸座(18)的上面连接在升降气缸轴端,旋转气缸座(18)的对角位轴式连接着旋转气缸(19),旋转气缸(19)通过具有固定角度的连接板(20)连接着手指气缸(21)。
全自动内外螺丝加工机
技术领域
本发明涉及一种管螺纹自动化加工设备,特别是一种全自动内外螺丝加工机。
背景技术
目前,加工可锻铸铁管件的内、外螺丝都是采用普通的双头攻丝机,这种攻丝机是在主机的中间部位装有卡具,卡具左右两边各有一个攻丝头,管件装卡到位后,左右攻丝头旋转进尺完成内、外螺纹加工,由于这种攻丝机是由工人在卡具和攻丝头不停地反复运动中手工完成管件的装卡,极易发生伤手事故,为避免伤手,操作者必须手持专用铁钳夹住管件进行装卡操作,即使如此,操作时稍有疏忽就有伤及操作者的危险,由此可见,现有的内外螺丝加工设备不仅工作效率低,劳动强度大,而且存在生产安全隐患。
发明内容
为克服传统式内外螺丝加工设备工作效率低,劳动强度大,易发生安全事故的缺陷,本发明提供一种全自动内外螺丝加工机。
本发明的技术方案是,全自动内外螺丝加工机由控制系统、加工系统、振动供料系统、振动运料系统、移料系统组成:
控制系统采用PLC程序实现对相关部件工作状态的自动控制;加工系统设置在机台上的加工位,包括内丝攻丝头、外丝攻丝头、固定卡具,内、外攻丝头相对设置在同一轴线上,内、外攻丝头之间设置有固定卡具;振动供料系统位于整机一侧,包括供料振动源、振动供料盘,振动供料盘固定在供料振动源之上,振动供料盘中设计有螺旋状走料路径,振动供料盘的走料路径终端与振动运料通道的进料端相衔接,在走料路径终端设计有选料段;振动运料系统设置在机台上,包括振动运料通道、运料振动源、挡件气缸、挡件闸板、检测开关,振动运料通道的进料端与振动供料盘的走料路径终端相衔接,振动运料通道的底部固定有运料振动源,挡件气缸通过支板设置在振动运料通道出料端的上方,挡件气缸连接有挡件闸板,检测开关设置在振动运料通道出料端的下面;移料系统设置在机台上与振动运料系统左右相对,包括立架、伺服电机、横向滑轨,还包括由滑动架、同步带、升降气缸、旋转气缸座、旋转气缸、连接板、手指气缸构成的机械手,立架上固定有伺服电机和横向滑轨,滑动架滑动设置在横向滑轨上并连接着伺服电机轮上的同步带,滑动架的上方固定有升降气缸,旋转气缸座的一侧滑动设置在滑动架一侧的纵向滑轨上,旋转气缸座的上面连接在升降气缸轴端,旋转气缸座的对角位轴式连接着旋转气缸,旋转气缸通过具有固定角度的连接板连接着手指气缸。
所述振动供料系统是通过供料振动源对振动供料盘的振动力,推动管件自动沿螺旋状走料路径进入振动运料通道;
所述选料段其特点是走料路径到此变成了侧向浅槽,当管件走到此段时可以实现自动选择料口方向,以保证进入振动运料通道的管件的料口方向一致,因管件的一端是待攻内丝的大外径料口,而另一端则是待攻外丝的小外径料口,当管件沿走料路径走到选料段时,小料口朝外的管件会被振动着顺利进入振动运料通道,而大料口朝外的管件会因为大料口一端失重而自动跌落到振动供料盘中继续待选;
所述振动运料系统,是把进入振动运料通道的管件,由运料振动源的振动力,推动管件沿振动运料通道继续前行,当第一个管件走到振动运料通道末端的机械手取件位置并被检测开关检测到时,挡件气缸使挡件闸板落下挡住后面继续前行的管件,以便机械手夹取检测到的管件;
所述移料系统是将管件移到加工位,当检测开关检测到有管件到达机械手取件位置时,挡件闸板下落,机械手下移将检测到的管件夹紧后提升到合适高度,在同步带的带动下平移到加工位上方,尔后旋转气缸带动手指气缸旋转90°后,机械手被升降气缸推动下移将管件送到固定卡具内后,返回取件位置的上方;
所述加工系统,是固定卡具卡紧加工管件后,由内丝攻丝头、外丝攻丝头从两头同时旋转进刀完成管件两头内、外螺丝的加工。
本发明实现了管件内外螺丝加工的全自动化,摒弃了频繁的手工装卡操作方式,与普通的双头攻丝机相比具有以下特点:
1、自动化程度高,可大幅提高加工效率,节省生产成本,一个操作工可同时操控4台机床,提高工作效率3-4倍,节省工资开支60%以上;
2、机器动作精准,可提高优质品率,减少废品损失3%以上;
3、可避免伤手事故,消除生产安全隐患。
附图说明
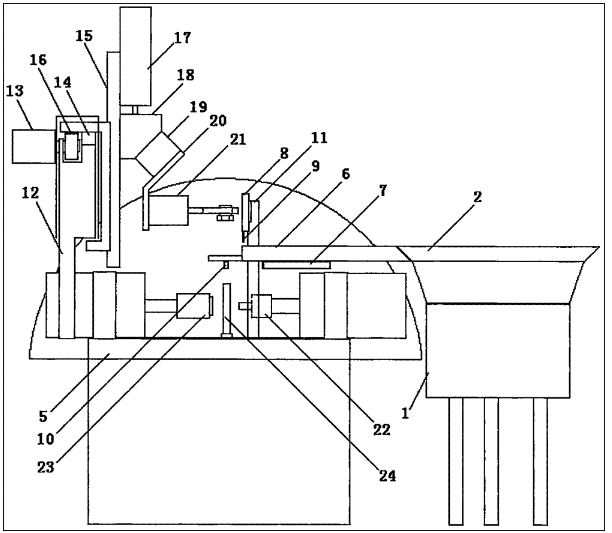
图1是本发明的正视图,图中机械手处于平行夹起管件上移的状态;
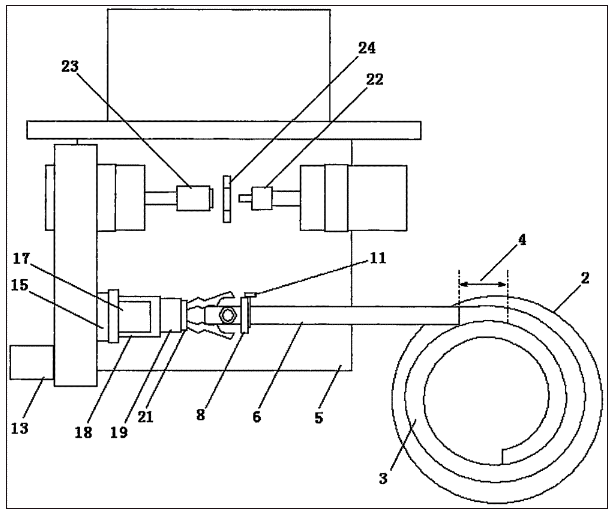
图2是本发明的俯视图,图中机械手已下移到振动运料通道末端的机械手取件位置欲夹取被检测到的管件。
图中:供料振动源1、振动供料盘2、走料路径3、选料段4、机台5、振动运料通道6、运料振动源7、挡件气缸8、挡件闸板9、检测开关10、支板11、立架12、伺服电机13、横向滑轨14、滑动架15、同步带16、升降气缸17、旋转气缸座18、旋转气缸19、连接板20、手指气缸21、内丝攻丝头22、外丝攻丝头23、固定卡具24
具体实施方式
下面对照附图通过实施例对本发明进行详细描述。
如图1、2所示,本发明全自动内外螺丝加工机由控制系统、加工系统、振动供料系统、振动运料系统、移料系统组成:
控制系统采用PLC程序实现对相关部件工作状态的自动控制;加工系统设置在机台5上的加工位,包括内丝攻丝头22、外丝攻丝头23、固定卡具24,内、外攻丝头相对设置在同一轴线上,内、外攻丝头之间设置有固定卡具24;振动供料系统位于整机一侧,包括供料振动源1、振动供料盘2,振动供料盘2固定在供料振动源1之上,振动供料盘2中设计有螺旋状走料路径3,振动供料盘2的走料路径终端与振动运料通道6的进料端相衔接,在走料路径3终端设计有选料段4;振动运料系统设置在机台5上,包括振动运料通道6、运料振动源7、挡件气缸8、挡件闸板9、检测开关10,振动运料通道6的进料端与振动供料盘2的走料路径终端相衔接,振动运料通道6的底部固定有运料振动源7,挡件气缸8通过支板11设置在振动运料通道6出料端的上方,挡件气缸8连接有挡件闸板9,检测开关10设置在振动运料通道6出料端的下面;移料系统设置在机台5上与振动运料系统左右相对,包括立架12、伺服电机13、横向滑轨14,还包括由滑动架15、同步带16、升降气缸17、旋转气缸座18、旋转气缸19、连接板20、手指气缸21构成的机械手,立架12上固定有伺服电机13和横向滑轨14,滑动架15滑动设置在横向滑轨14上并连接着伺服电机轮上的同步带16,滑动架15的上方固定有升降气缸17,旋转气缸座18的一侧滑动设置在滑动架15一侧的纵向滑轨上,旋转气缸座18的上面连接在升降气缸轴端,旋转气缸座18的对角位轴式连接着旋转气缸19,旋转气缸19通过具有固定角度的连接板20连接着手指气缸21。
实施例:
将管件装入振动供料盘2,开机,供料振动源1发出的振动力推动振动供料盘2内的管件沿走料路径3依次前行,当管件走到走料路径3终端的选料段4时,小料口朝外的管件被振动着进入振动运料通道6,而大料口朝外的管件会因为大料口一端失重而自动跌落到振动供料盘2中;当管件进入振动运料通道6时,振动运料通道6底部的运料振动源7产生的振动力推着管件前行,当第一个管件走到振动运料通道6末端的机械手取件位置并被检测开关10检测到时,挡件气缸8使挡件闸板9落下挡住后面继续前行的管件,以便机械手夹取检测到的管件;
挡件闸板9下落后,处于上方的机械手在升降气缸17的推动下下移,手指气缸21动作使其上的手指平行张开将管件夹紧,然后在升降气缸17的拉动下提升到合适高度,随之伺服电机13启动,通过同步带16的运转带动夹有管件的机械手平移到加工位上方,旋转气缸19带动手指气缸21旋转90°,使手指气缸21夹着管件的手指垂直朝下,管件与固定卡具24处于同轴状态,此时升降气缸17再次推动机械手下移,使管件进入固定卡具24内被卡紧,手指气缸21动作使其上的手指张开松开管件,随之在升降气缸17的拉动下机械手上移,旋转气缸19带动手指气缸21反向旋转90°,使手指气缸21的手指还原到水平状态,再由伺服电机13带动同步带16使机械手横移到取件位置的上方,被卡紧在固定卡具24内的管件由内丝攻丝头22、外丝攻丝头23从两头同时旋转进刀完成管件两头内、外螺丝的加工。